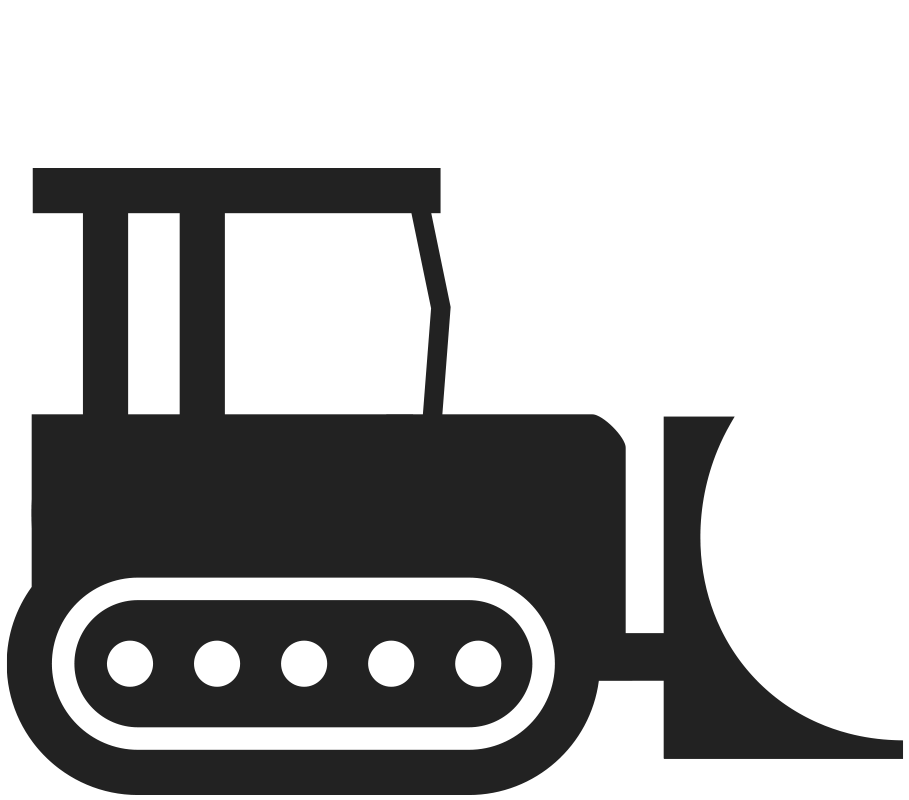
Plant and Equipment
Minimum RequirementsPlant includes machinery, equipment, appliances, containers, implements and tools and components or anything fitted or connected to the plant and equipment.
-
Limbs amputated by unguarded moving parts of machines
-
Being crushed by mobile plant
-
Sustaining fractures from falls while accessing, operating or maintaining plant
-
Electric shock from plant that is not adequately protected or isolated
-
Burns or scalds due to contact with hot surfaces, or exposure to flames or hot fluids.
-
Other risks include hearing loss due to noisy plant, and musculoskeletal disorders caused by poorly maintained plant and manually handling or operating poorly designed plant.
-
Energy sources are to be isolated when working on plant or it is not in use
-
Isolation locks are to be used at all times when conducting maintenance on plant
-
Plant operators are to be verified as qualified or competent in accordance with the PDI4-54 Training Matrix prior to commencing works
-
Critical documentation for the plant shall be obtained prior to commencing works, including service history, statutory registrations, plant risk assessment, Safe Work Method Statements (SWMS) and operators’ manuals
-
Pre-start inspections are to be conducted on all items of plant where required or recommended by the manufacturer
-
Spotters are to be in place in areas of operating mobile plant, with effective communication devices (e.g. radios)
Registration required |
Exemptions |
---|---|
− Boilers categorised as hazard level A, B or C according to criteria in section 2.1 of AS 4343–2005: Pressure equipment—hazard levels. − Pressure vessels categorised as hazard level A, B or C according to the criteria in section 2.1 of AS 4343–2005: Pressure equipment—hazard levels, except for gas cylinders; LP Gas fuel vessels for automotive use, and serially produced vessels − Tower cranes including self-erecting tower cranes. − Lifts, escalators and moving walkways − Building maintenance units − Amusement devices classified by section 2.1 of AS 3533.1–2009: Amusement rides and devices—Design and construction except amusement devices noted below − Concrete placing booms, and − Mobile cranes with a rated capacity of greater than 10 tonnes. |
− Any pressure equipment (other than a gas cylinder) excluded from the scope − of AS/NZS 1200–2000: Pressure equipment. See section A1 of Appendix A to AS/NZS 1200–2000 − A manually powered crane or hoist − A reach stacker − Amusement devices classified by section 2.1 of AS 3533.1–2009: − Amusement rides and devices—Design and construction that are: − class 1 devices − playground devices − water slides where water facilitates patrons to slide easily, predominantly under gravity, along a static structure − wave generators where patrons do not come into contact with the parts of machinery used for generating water waves, and − inflatable devices, other than inflatable devices—continuously blown—with a platform height of three metres or more |