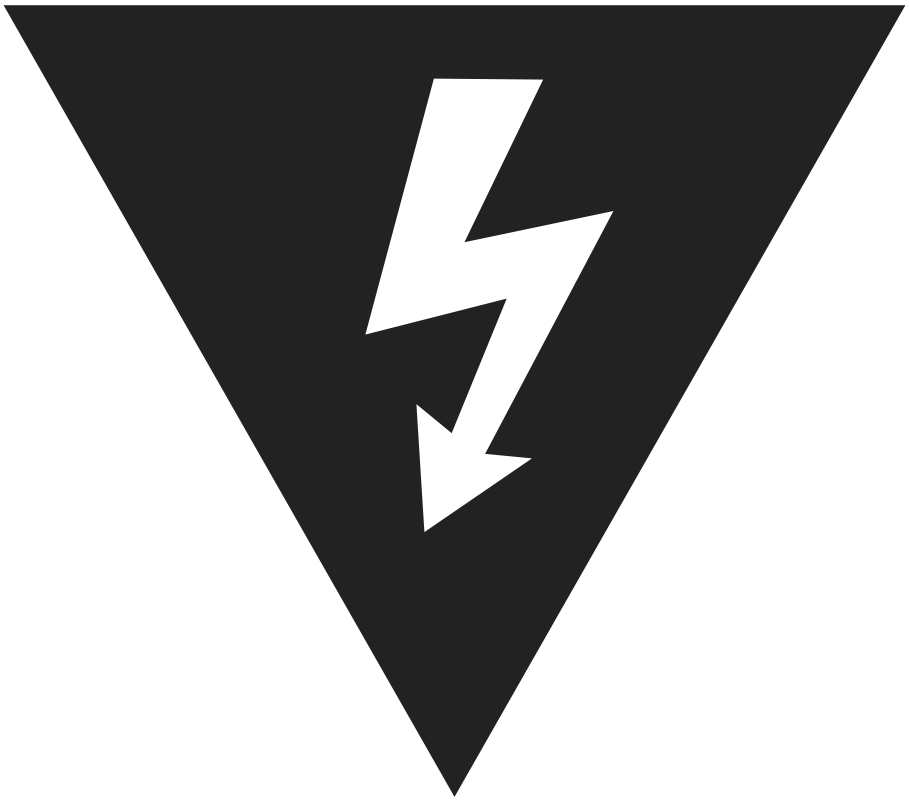
Electrical Services
Minimum RequirementsWork that involves connecting electricity supply wiring to electrical equipment or disconnecting electricity supply wiring from electrical equipment, or installing, removing, adding, testing, replacing, altering or maintaining electrical equipment or an electrical installation.
-
Barriers shall be used to control access to electrical circuits, including temporary barriers, or use of insulation for preventing an electrical path to earth
-
If there is a risk of damage to electrical wiring, a licenced electrical contractor is to ensure wiring is protected in accordance with Section 2.5.3 of AS/NZS 3012 Electrical Installations
-
Construction and Demolition Sites. RCD’s are to be in use at all times on site, with current test and tags
-
Temporary Distribution Boards shall be positioned in a manner that eliminates the need for flexible cords or cables to be run between levels
-
First aid and CPR qualified safety observers competent in Low-voltage rescue must be in place when live electrical work is being conducted
-
Metallic items or jewelry are not to be worn when performing work near exposed conductors
-
All persons conducting electrical work are to be appropriately trained and qualified
-
Only qualified electricians are to make isolations at an MSB or DB
-
Electrical apprentices must be provided supervision in line with NSW Fair Trading: Supervision Practice Standard for Apprentices in the Electrical Industry
Equipment Class |
Testing Interval |
Equipment Class |
Testing Interval |
---|---|---|---|
Construction wiring, Including switchboards |
Inspected and tested prior to energisation, then re-inspected (visually) every 6 months |
Portable RCD’s – push button test |
Before each use of equipment |
Temp Distribution boards RCDs |
Monthly / with trip times |
Re-locatable structures, fixed and transportable equipment |
6 months |
Portable equipment and flexible electrical cords (extension leads) |
3 months |
Portable RCD’s – operating time |
3 months |
Equipment in amenities and site offices |
3 months |
Fixed RCD’s operating time |
12 months |