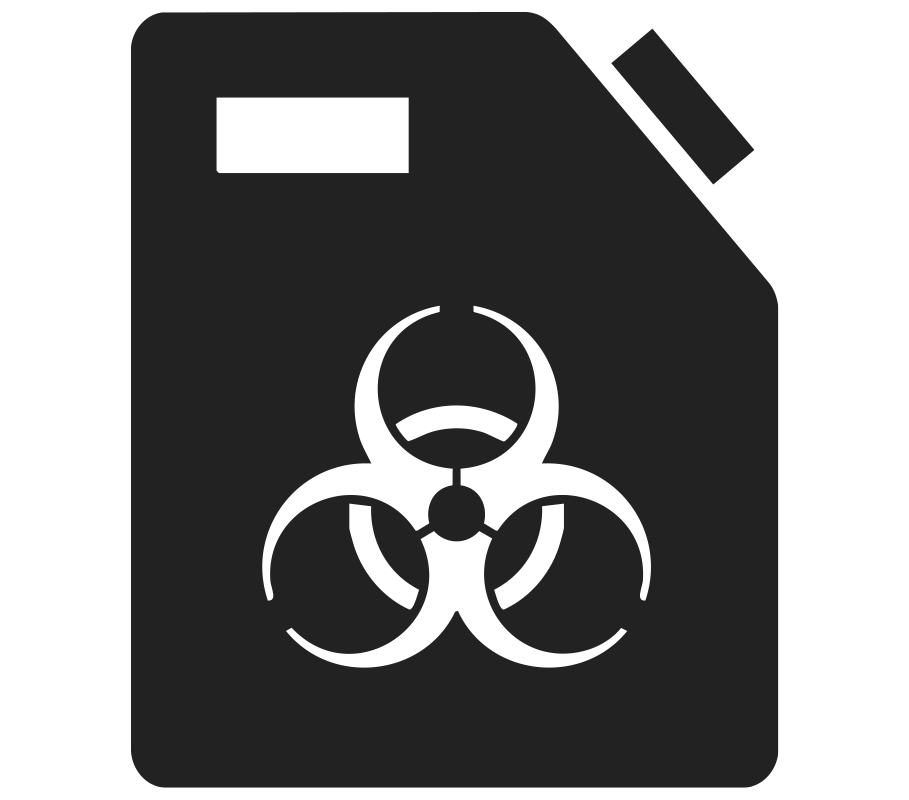
Hazmat Removal & Chemicals
Minimum RequirementsA hazardous material is any item or agent (biological, chemical, radiological, and / or physical) that has the ability to cause harm to humans, animals, property and/or the environment
-
Leave hazmat in place, do not disturb, encapsulate via remote means
-
A clearance certificate is to be obtained prior to workers entering any area where hazardous materials have been removed under the project
-
The hazards associated with substances shall be considered as part of their selection (e.g. using nonflammable paints or adhesives).
-
Erect fully sealed enclosures to separate hazmat removal work from work area
-
Seal hazmat to leave in place or prior to removal
-
Barriers, exclusion zones, signage and / or traffic management is to be in place where work with hazardous substances or materials can impact other persons and / or the environment
-
Hazardous substances / dangerous goods are to be stored in a segregated cabinet or area inline with the associated Safety Data Sheet (SDS), with appropriate signage, ventilation, drainage, containment and / or bunding
-
Use of HEPA filtered H-class industrial vacuum cleaners to remove hazmat dusts and debris
-
Spray equipment includes wet sprays with water mist or wetting solution. A constant low- pressure water supply is required for wetting down asbestos and related items to suppress airborne asbestos fibers
-
Soak the asbestos until total saturation is achieved prior to removal
-
An appropriate class and sized spill kit is to be on-site when quantities of hazardous substances are being stored or used
-
When working with hazardous materials all tools and equipment should be used in conjunction with attachments or mechanisms for encapsulation, capture or suppression of air-borne fibers
-
Equipment used for monitoring purpose (e.g. gas monitors) are to have records of calibration check before use
-
All personnel using or interacting with hazardous materials or substances must be provided information, training and supervision
-
Emergency management plans shall consider the specific hazmat, its associated hazards and procedure required to control it and affected workers
-
Hazmat removal contractors (e.g. Asbestos removalists) must be appropriately licenced
-
Health monitoring shall be undertaken when workers’ health is at risk following possible exposure.
-
Current Safety Data Sheets (SDS) are to be obtained for all hazardous substances used or stored on site
-
Hazardous waste disposal records are to be retained on site throughout the project
-
All PPE used for the removal of asbestos should be inspected before the commencement of the asbestos removal work, after it undergoes any repairs and at least once every seven days when it is continually being used
-
A register with the details of these inspections, the state of the equipment and any repair details should be maintained
-
At the end of the asbestos removal work and upon leaving the asbestos removal work area you must ensure that all PPE is disposed of as asbestos waste
-
PPE should be thoroughly wet before being placed in bags
Type of licence |
What asbestos can be removed? |
---|---|
Class A |
Can remove any amount or quantity of asbestos or asbestos-containing materials (ACM), including: − any amount of friable asbestos or ACM − any amount of asbestos-containing dust or debris (ACD) − any amount of non-friable asbestos or ACM. |
Class B |
Can remove: − any amount of non-friable asbestos or ACM − any amount of ACD associated with the removal of non-friable asbestos or ACM. |
No Licence |
Can remove: − Up to 10m2 of non-friable asbestos or ACM − ACD that is: − associated with the removal of less than 10 m2 of non-friable asbestos or ACM − not associated with the removal of friable or non-friable asbestos and is only a minor contamination. |