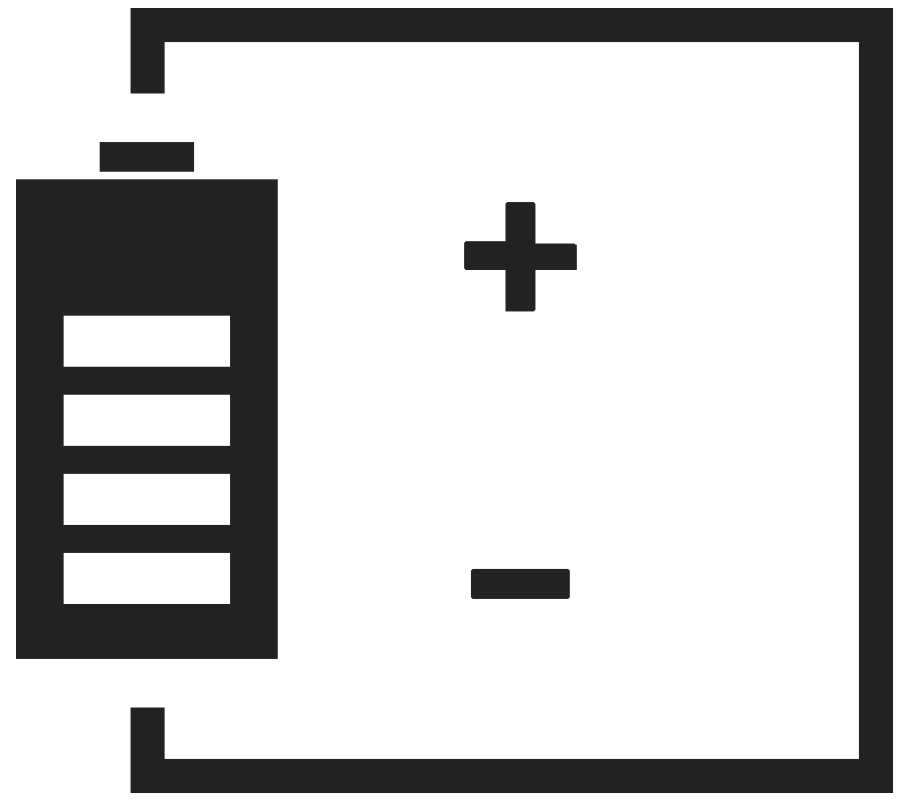
Stored Energy
Minimum RequirementsStored energy refers to the potential energy that is stored in an object or system. Different forms of stored energy include mechanical, electrical, thermal, chemical, and gravitational energy.
-
Hydraulic works
-
Compressed air lines
-
Electrical works
-
Works on pumps or pipes
-
Work on powered plant, fixed or mobile
-
Lock-out Tag-out (LOTO) processes are to be documented and applied for all isolations
-
Dual isolation methods are to be implemented where practical, e.g., the use of blanking plates
-
Barriers shall be used to control access to areas where stored energy sources are being worked on, including temporary barriers
-
Ensure machine guards, barriers and interlocks are functional as designed prior to commencing works
-
RCD’s are to be in use at all times when using power tools
-
All persons conducting isolations of stored energy sources are to have relevant training or qualifications for the works
-
A Baseline Isolation Permit is to be approved prior to commencing works
-
Work planning should consider exposure pathways, including inhalable gases, safe approach distances and Workplace Exposure Standards (WES)
-
No vehicle, machine, equipment, or process is to be operated when any tag or lock (Personal, Isolation, Out of Service) is attached
Energy Sources |
Energy Sources |
---|---|
Electrical |
Pneumatic |
Water |
Natural Gas |
Chemical and Coolant |
Hydraulic |
Steam |
Mechanical |