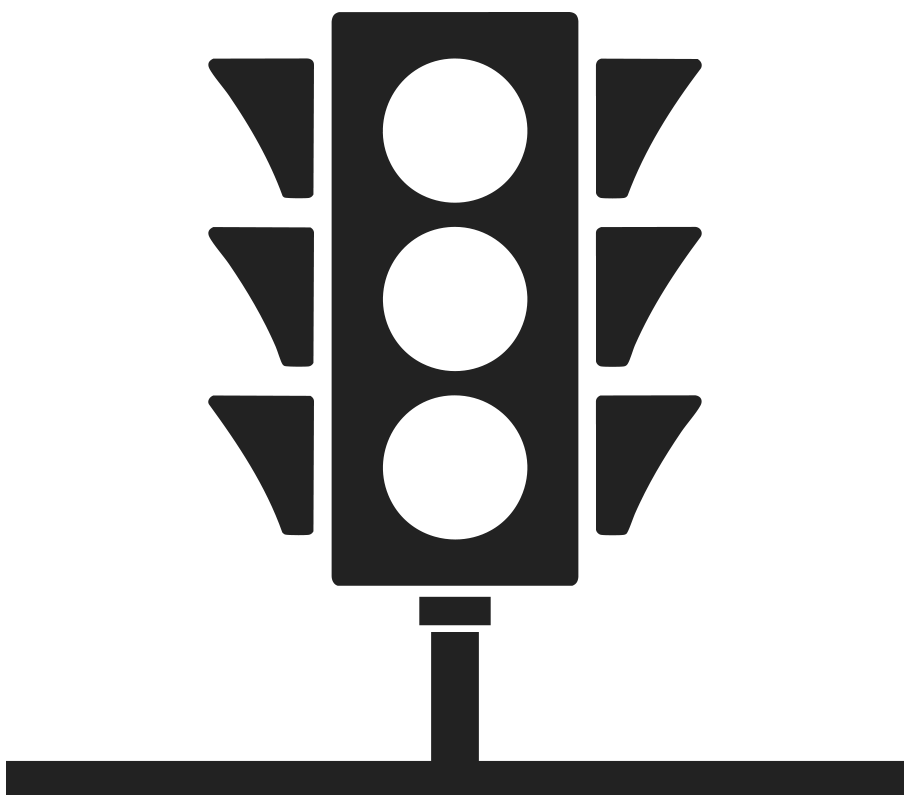
Traffic Management
Minimum RequirementsTraffic Management Plans are to eliminate or minimise the risk of injury from the interface between vehicle movements in and out of the workplace (site) and members of the public (pedestrians, road users)
-
Being hit by a vehicle;
-
Being trapped between a vehicle and a structure;
-
Vehicles colliding with each other or a structure;
-
Injured as a result of improper use of a vehicle;
-
Exposure to unsafe levels of fumes or excessive noise from vehicles.
-
Exclusion zones: There must be adequate separation between vehicles and members of the public as well as Traffic Controllers. Vehicles, members of the public and Traffic Controllers should be adequately protected through the use of
-
hard barriers, fences or guardrails with safe access routes and no-go zones established; high impact barriers (e.g. modular concrete/steel/water-filled barriers or an earth berm)
-
temporary physical barriers using: barricade tape or mesh; traffic cones; signs; flashing lights; reflective markers e Safe escape routes are in place for traffic control personnel interacting with live traffic
-
Where possible, designate specific parking areas for workers and visitors outside of construction area
-
Parking: implement reverse parking where possible; located away from busy work areas and traffic routes; have walkways leading to and from parking areas separated from vehicles or vehicle routes; be clearly marked and sign-posted, well-lit and unobstructed
-
Traffic electronic signage (variable speed signs, speed detection displays) is considered for community alerts, upcoming works, and speed controls
-
Pedestrian routes / crossings: Where pedestrians are required to cross vehicle routes the following methods to manage the risk are to be used: a Traffic Controller directing traffic; ground markings, lights or signs; or crossings points where pedestrian’s cross busy circulation roadways
-
All vehicles to be inspected as fit for purpose including warning devices, emergency stops, flashing lights, reverse beepers, seatbelts, lights, and horns, prior to the commencement of work
-
All person(s) operating plant or vehicles are to complete the site / workplace specific driver induction and records of that induction to be kept onsite
-
All vehicle and plant operators to hold the correct licences, in accordance with the Training Matrix
-
Toolbox talks to be completed to assess and adjust controls based on daily conditions e.g., weather, traffic volume, visibility etc
-
A Traffic Management Plan (TMP) must be submitted to the Airfield Operations and Works Coordinator in the event any works which may have an impact on any airside roads including Apron Service Roads, Airside Road or Perimeter Road
Certification requirements |
Certification requirements |
---|---|
Traffic Management Plan and Traffic Control Plan development |
RIICWD503E – Prepare traffic management plans and traffic guidance schemes |
Traffic Controller (only) Restricted to only controlling traffic with a Stop Slow Bar |
RIISS00054 – Traffic Controller |
Traffic Control Supervisor |
RIISS00043 – Work Zone Traffic Control |