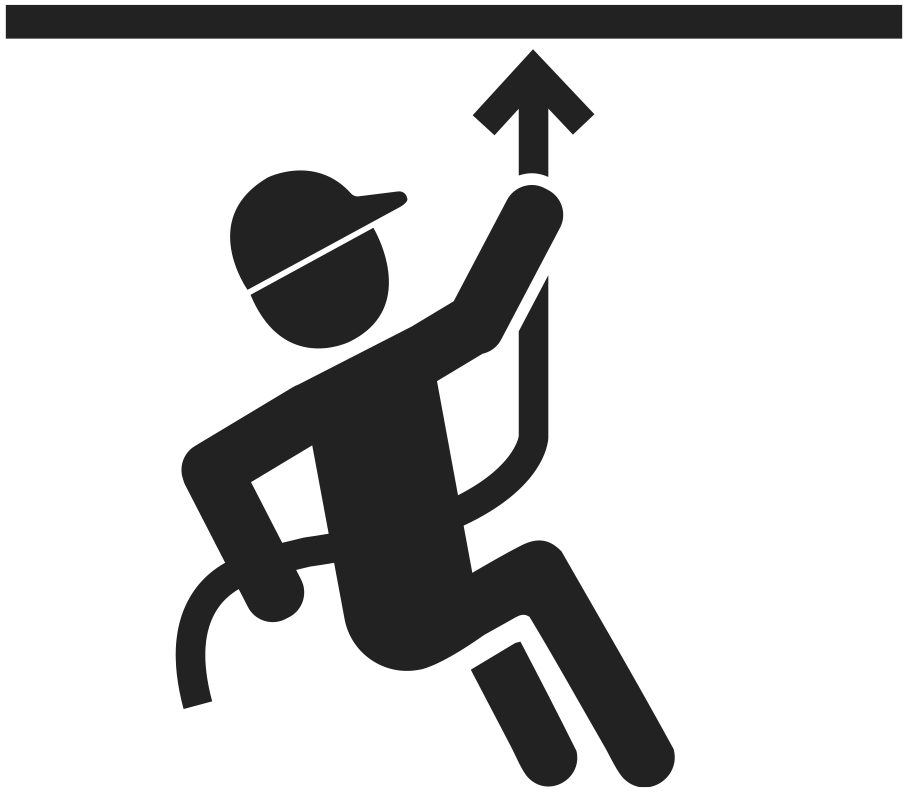
Work at Heights
Minimum RequirementsFall hazards are associated with many construction work activities e.g. scaffolding, formwork, roofing, height access systems, equipment and plant, unloading trucks, and demolition works.
Falls hazards can also be present at ground level e.g. excavations, penetrations, service pits, shafts and risers
-
Fall prevention devices such as scaffolding, edge protection, temporary work platforms
-
Work positioning systems such as fall restraint systems
-
Fall arrest systems such as catch platforms and inertia reels
-
Where ladders are required to undertake works, platform ladders shall be utilised
-
Where another form of ladder is required for the works, i.e. straight ladder, a risk assessment shall be undertaken and approved by the Site Manager prior to works commencing
-
Exclusion zones are to be in place under and around all working at heights work activities to isolate personnel from object fall from height hazards and risks
-
Ensure certified roof safety mesh in accordance with AS/NZS 4389 has been installed prior to roof works or access over potentially brittle roof materials
-
Overhead protection to be installed to protect exposed services, plant, equipment and trafficable areas Penetrations covers to be installed / managed in accordance with HRS – Temporary Structures
-
Provide safe means of access and egress from the workplace or any area within the workplace from or through which a person could fall, such as a platform or scaffolding
-
Catch nets, mesh blankets, tool / equipment lanyards shall be used individually or in conjunction based on a risk assessment where exclusion zones will not adequately manage object fall from height hazards and risks
-
Secondary guarding/devices on Mobile Elevating Work Platforms (MEWP) controls to prevent crush injuries during operation
-
Risk assessment to be undertaken to determine use of spotters and / or exclusion zones to manage object fall from height hazards and risks
-
Ground and weather conditions are to be assessed prior to working at heights for potential impacts to stability of working at heights plant and equipment e.g., ladder instability, EWP roll-over
-
Overhead hazards are to be identified and controls implemented prior to commencing works e.g., safe approach distances for powerlines
-
Work at heights permits shall be approved prior to commencing works above 2m (excluding work from platform ladders and working from inspected and approved scaffold)
-
When working in harness, fall restraint systems shall be utilised as first preference. If not practicable for scope of works, fall arrest system shall be utilised and rescue plan developed
Equipment |
Frequency |
Competency |
Record |
---|---|---|---|
Anchor Points - Temporary |
Visual inspection of Anchor and parent structure: 30 days |
SB, SI, SA, RB, RI, RA, Trained in Working Safely at Heights and installed as per manufacturer’s instructions. |
Evidence of Working Safely at Heights training Evidence of system being proprietary |
Anchor Points – Permanent & Static lines |
12 months |
SB, SI, SA, RB, RI or RA or workers trained in use of the system |
Compliance certificate |
Fall arrest devices |
12 months |
RIIWHS204E |
Service/ inspection tag and next test date |
Harnesses/Lanyards / Ropes and slings |
Before/after use and 6 monthly |
Work at Heights - RIIWHS204E |
Service/ inspection tag and next test date |
Ladder - Portable |
Before each use. After drops and impacts. |
N/A |
Service/ inspection tag and next test date |
Ladder - Fixed |
In accordance with affixed installation record |
SB, SI, SA, RB, RI or RA or workers trained in use of the system |
Service/ inspection tag and next test date |